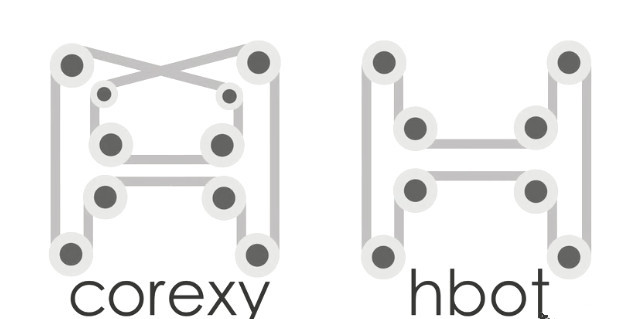
The 3D printer with CoreXY structure is shown in the figure:
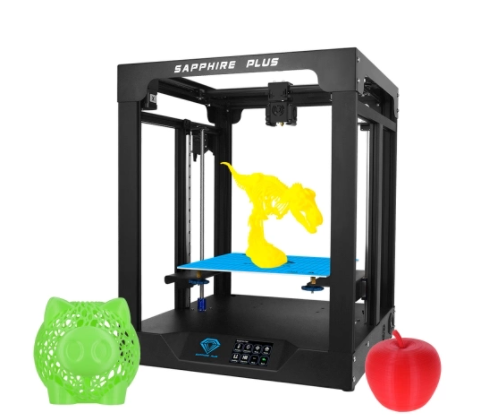
The 3D printer with Hbot structure is shown in the figure:
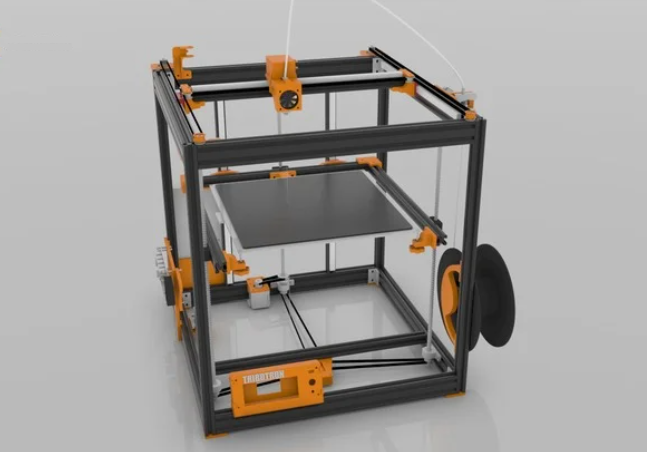
CoreXY structure is not used much in 3D printers. Compared with 3D printers based on Cartesian structure, it has more advantages. The two conveyor belts on this machine are also interesting. They appear to intersect, but they are actually on two planes, one on top of the other. Two stepping motors are installed on the carriage moving in the X and Y directions, which makes the movement of the carriage more precise and stable.
The principle of CoreXY is to control the movement of XY through two motors at the same time. When the left and right motors are in the same direction, they move to the X axis, and when the two motors are in reverse, they move to the Y axis. With the simultaneous action of two motors, the force is more stable than a single motor controlling one axis, and it can also reduce the weight of a motor on the XY platform.
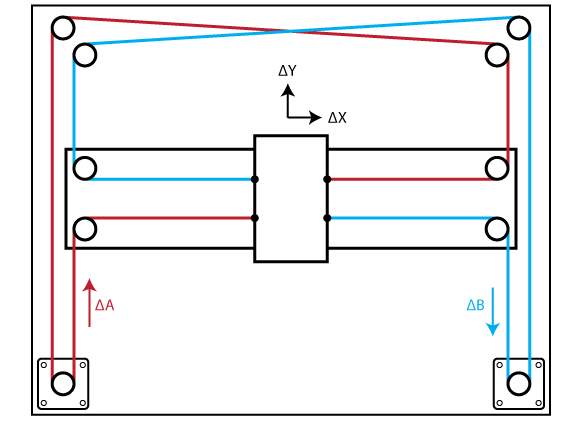
Hbot structure, from the top view, the XY motion mechanism of the machine is similar to the letter “H”. Different from the cross-axis, I3, and makerbot machine structure, the Hbot structure is fast, without the burden of the X-axis motor moving together, and it can be made smaller and the printing area is higher.
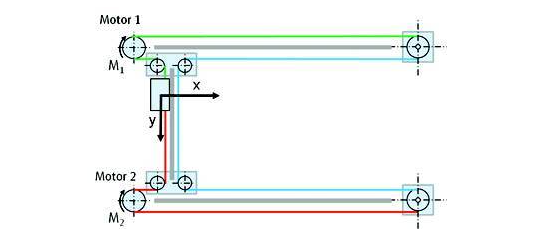
CoreXY and Hbot structures are common two-arm parallel structures. No matter XY motion requires the cooperation of two motors, it is called parallel.
There are three main differences between CoreXY and Hbot structure:
1. Depending on the installation of the slider, the CoreXY structure slider can be connected to two layers of belts. The reason is that the upper and lower belts move in the same direction, while the Hbot structure slider can only be connected to one layer (up/down). The reason is that the upper and lower belts move in opposite directions.
2. The winding path of the belt. The characteristic of the Hbot structure is that the winding is very simple, and only one belt is needed for the whole circle, and it is on a flat surface. However, this kind of Hbot also brings structural problems, as shown in the figure:
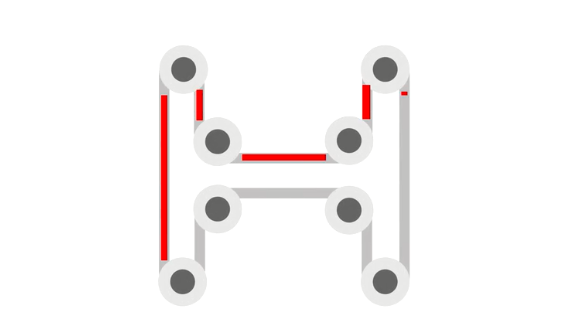
The CoreXY structure requires two belts. Because the belts are crossed, they need to be installed in two different planes. The complex structure also brings some structural advantages, as shown in the figure:

The force of the crossbar is different. First, you need to explain the principle of force analysis. First, the belt is a flexible material. The flexible material can only provide pulling force but not thrust. Using this principle, you can analyze the force of each point. When hbot moves along the y-axis of the slider, at this time, the two pulleys on the lower layer of the beam have no power. Because the belt is pushing the pulley at this time, and the belt cannot provide thrust. The above two are pulled, so there is power, so the beam moving along the y axis is balanced by force, as shown in the figure:
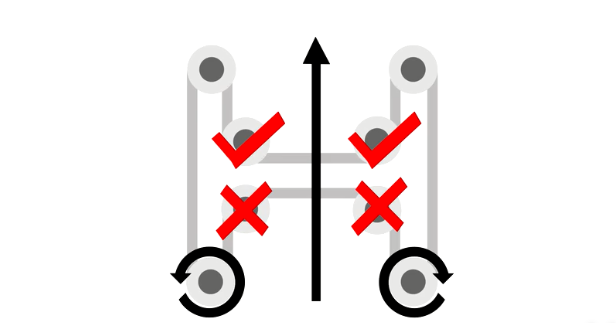
When the slider moves along the X axis, the results obtained by the same analysis method are shown in the figure:
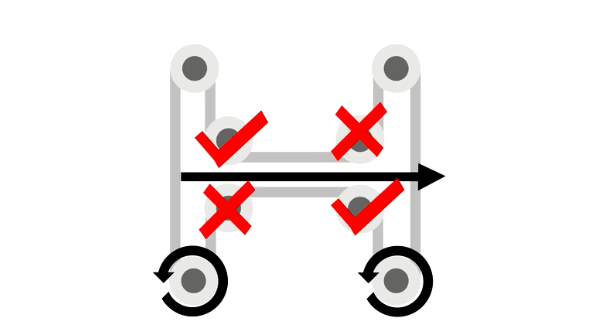
It can be found that the force of the beam is not in a straight line, and it can be found that the force of the beam is not in a straight line, which will generate torque, squeeze the track, and be affected vertically.
In the CoreXY structure, the force on the movement along the Y-axis is the same, the force at this time is on a straight line, so the XY motion and the force on the beam are balanced, while the force on the X-axis is shown in the figure:
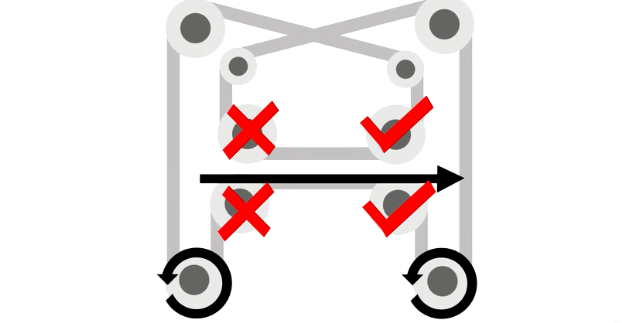
Motor installation position
In theory, as long as they are installed on both sides of the beam, Hbot is usually installed on the same side in actual use.
This looks more beautiful. However, there are more choices for the motor installation position of CoreXY structure.
Common problems and solutions
1. The belt is too long, the size of the machine is too large, and the belt is too long to cause great deformation. The solution is to use a thicker and wider belt and try to tighten it as much as possible.
2. Hbot structure stress problem, the first solution is to reduce the width of the beam and reduce the moment arm. Method 2: Use high-strength sliders and rails on both sides of the beam to reduce deformation.
Using these two types of printers, high-speed and high-precision printing can be achieved. The installation is relatively simple and the cost is not high.